Starting with spare parts, 3D printing poised to transform car sector
By DPA | 01 November 2020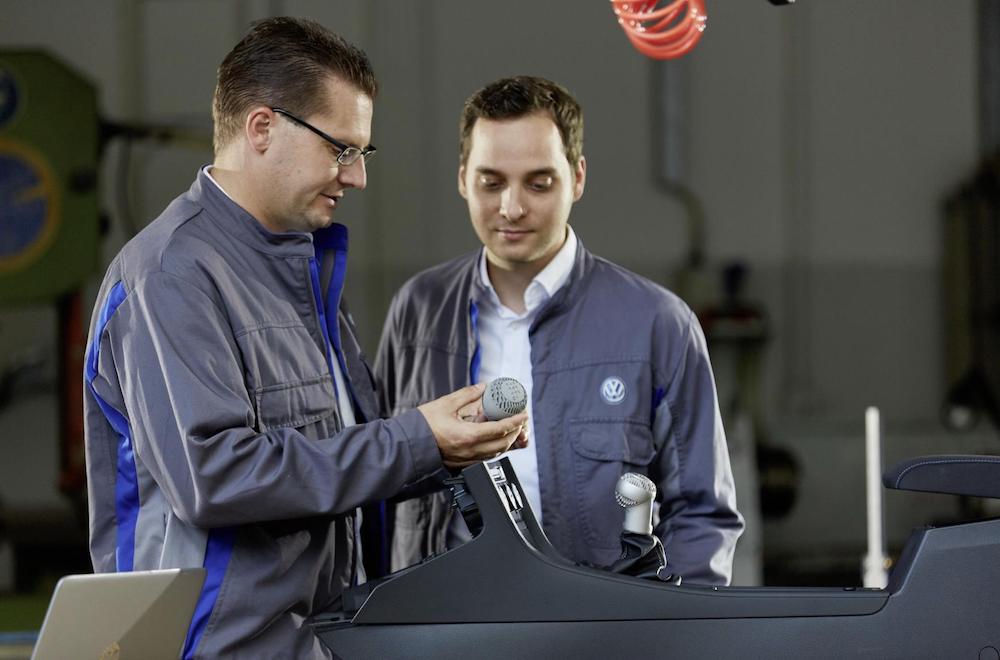
BERLIN: A broken plastic lever or worn-out cog for the windscreen wiper motor: Certain spare parts are either hard to find or not available at all. The only thing that helps is a custom-made product.
However, components in small quantities usually cost more and might require the use of a special tool that itself would have to be made. The situation is different for parts from 3D printers or direct metal laser sintering (DMLS), also known as additive manufacturing.
"Printed parts are profitable for small quantities or even a single piece, as there are no expensive initial costs for the tool," says Philip Kalaydjiev, founder of a start-up for printed car parts.
"Customers usually send us an old spare part, often one that's faulty, worn-out or mirror-inverted, and we produce a digital 3D scan for printing later on," explains Kalaydjiev. Customers include vintage car collectors, amateur mechanics, professional garages and dealers who need spare parts manufactured in large quantities.
Parts can be printed in rubber, plastic, tool steel, stainless steel and aluminium alloys. "Spare parts made of one material are easy to print - even sleeves or thread can be cut into the material afterwards. But with hybrid components made from different materials, a printer reaches its limits. Not everything can be produced yet," explains Kalaydjiev. The strength can be controlled by the thickness of the layers and the material quality so that the result is equivalent to parts made by conventional manufacturing processes.
The price per part depends on the geometry of the component and the volume. "The more complex a part is, the more time-consuming it is to create the 3D model. The thicker the part is, the more material is applied, with the printing taking longer," explains Kalaydjiev.
Printed parts are well-suited for geometrically complex parts with radii, grids or holes, says Dirk Baehre, a professor of manufacturing technology. "For very precise components, such as in the powertrain, 3D printing reaches it limit. Unless manufacturers have classified and approved this form of production, printed parts must not be used in load-bearing and safety-relevant areas," he explains.
However, Baehre considers 3D plastic printing to be very interesting in both the hobby and private sectors: "It can be used to print small objects, decorations or repairs that are not relevant to safety."
Manufacturers such as BMW, Bugatti, Mini, McLaren, Porsche and Seat already use components made by 3D printers for new cars. Porsche, for example, produces pistons, while Bugatti produces exhaust trims. BMW recently invested 15 million euros in a new campus for 3D printing.
Jan Dannenberg from consultancy firm Berylls Strategy Advisors also sees several advantages to 3D print production: "It's economical to produce components up to around 500 units using 3D printing because no separate moulds or tools have to be made for this. It's only at higher volumes that conventional processes such as injection moulding or aluminium casting have a cost advantage."
Printed parts are therefore often used for prototypes or small batches, explains Dannenberg. In addition, different geometrics and features can be integrated, which offer high stability in a small space and thus a high load with low material usage.
According to Dannenberg, however, only the next generation of 3D printers will be able to print faster, more economically for high volumes, and larger components. Only then will production, which is still rather unusual today, become the standard - and not just for an old, worn-down interior mirror or a faded dashboard.
Tags
Autos News
Reviews
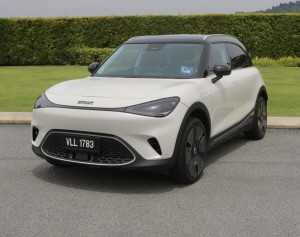
8.8
smart #1 (Premium): Agile, engaging, roomy, premium motoring
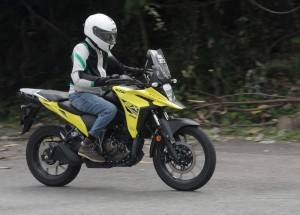
6.6
Suzuki V-Strom 250 SX: Multi terrain warrior
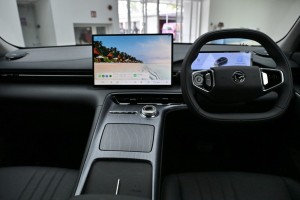
Proton e.MAS 7 impresses in quick dynamic driving exercises
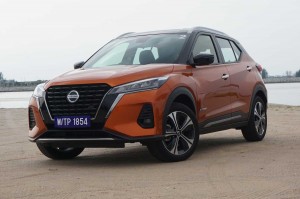
Nissan Kicks e-Power: Kicking off a new efficiency
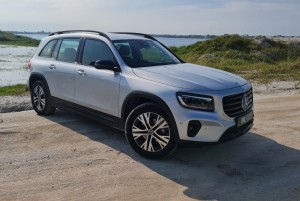
6.8
Mercedes-Benz GLB 200: Measured versatility
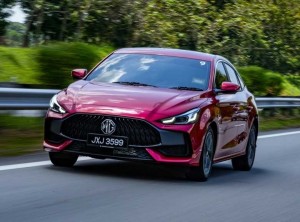
MG5: Slick and comfortable cruiser
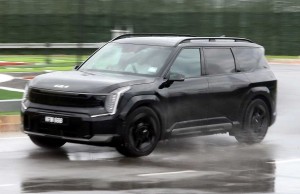
8.2
Kia EV9: Prime cut
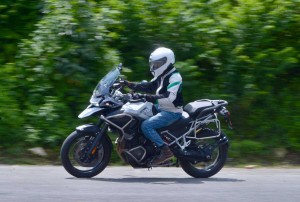
8.0
Triumph Tiger 1200 GT Pro: High adventure on two wheels
Videos
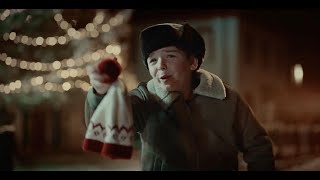
The Snowball – Lamborghini’s Heartwarming Christmas Story of...

EVOGO battery swapping solution showcased at IAA Mobility 20...

Jaguar's Bold Type 00 Concept: A Glimpse into the Future of ...
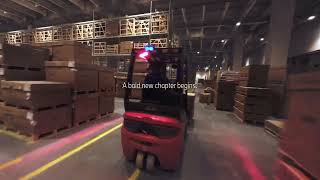