MUNICH: BMW Group has announced the production of round battery cell samples at its new Cell Manufacturing Competence Centre (CMCC) in Parsdorf near here.
These samples, to come in two versions, will be used in the models of the Neue Klasse from 2025 onwards, showcasing BMW's leading role in battery cell technology.
The CMCC will enable the company to span the entire cell value creation process, setting benchmarks for production, quality, performance, costs, and environmental standards.
The facility has received a total investment of around €170 million (RM859mil) and is supported by the German Federal Ministry of Economic Affairs and the Bavarian Ministry of Economic Affairs, Regional Development, and Energy.
One of the key focuses of the CMCC is recycling and circularity.
The BMW Group aims to efficiently and responsibly use raw and carrier materials in cell production, as they are significant cost factors.
The facility will collect residual materials from the production process, sort them, and feed them back into the cell production cycle.
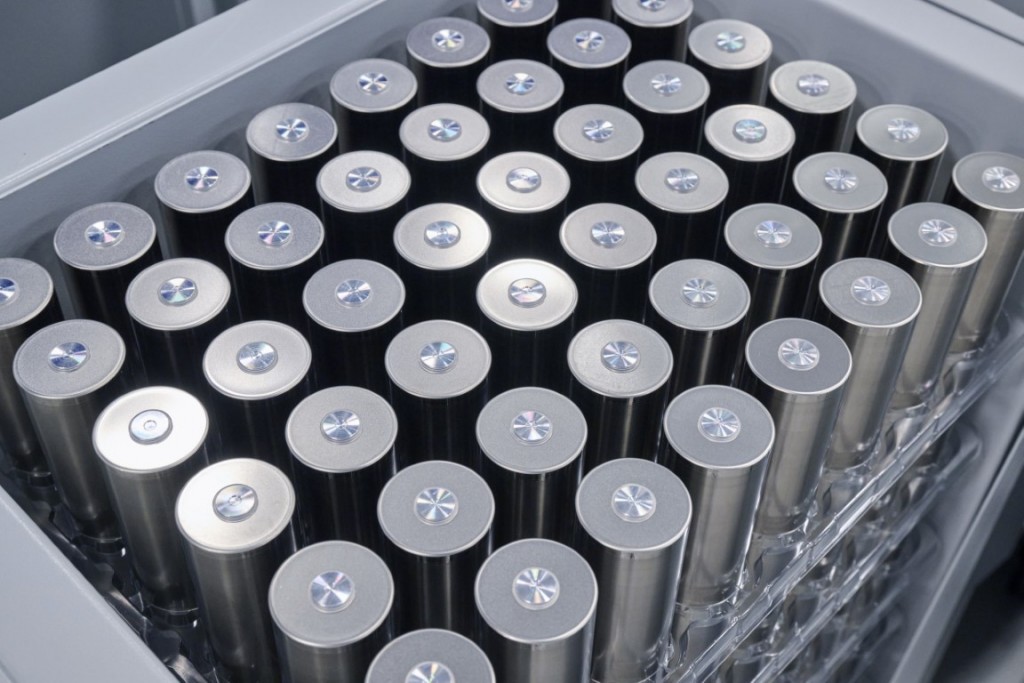
Additionally, BMW Group experts are working on reusing materials and components from the entire battery after its initial use in the vehicle.
The long-term aim is to reuse all raw materials in recyclable high-voltage batteries.
The production process for battery cells at the CMCC involves several steps. It begins with electrode production, where the base materials are mixed and coated onto metal foils.
The coated foils are then wound into "jelly rolls" and inserted into the cell housing. The cells are filled with electrolyte, charged, and checked for functionality and quality.
The CMCC in Parsdorf is built to high environmental standards, with a focus on sustainability.
It will operate fossil-free, relying on electricity produced using renewable energy sources. The building will also be supplied with regenerative heat produced using state-of-the-art groundwater and air heat pumps.
The battery cells produced at the CMCC will be part of the sixth generation of BMW battery technology.
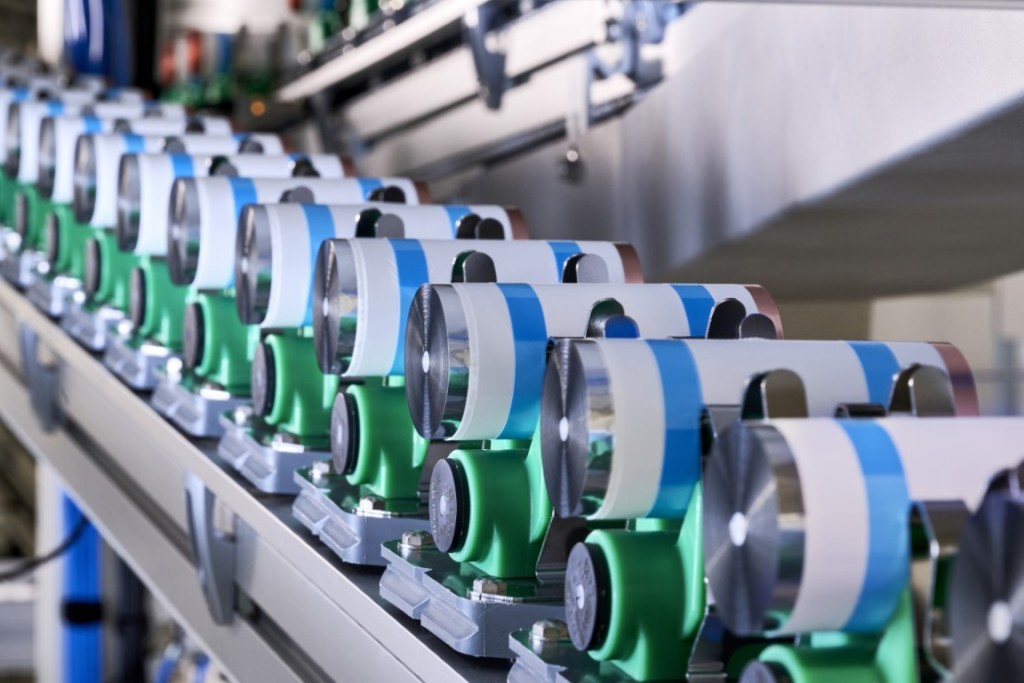
These cells will have a new round format (46mm diameter by 95mm tall and 120mm tall versus Tesla's 4680 battery cells) and enhanced cell chemistry, resulting in a significant 30% increase in range, according to the WLTP cycle.
Compared to the prismatic cells of the fifth BMW battery cell generation, the nickel content of the sixth-generation BMW round cells will be higher on the cathode side, while the cobalt content will be reduced.
On the anode side, the silicon content will be increased, improving the cell's volumetric energy density by more than 20 percent. The Neue Klasse models will also have a higher voltage of 800 volts, optimising charging capacity and reducing charging time.
In terms of sustainability, the BMW Group is committed to reducing the carbon footprint and resource consumption of battery cell production.
The company will use cobalt, lithium, and nickel containing secondary material for standard production of battery cells. Additionally, its cell suppliers will use only green power from renewable energies in production, resulting in a reduction of the carbon footprint by up to 60 percent compared to the current generation of battery cells.
Overall, the production of battery cell samples at the CMCC in Parsdorf demonstrates BMW's commitment to advancing electromobility and its expertise in battery cell technology.
The facility's focus on recycling and circularity, as well as its sustainable building practices, further highlight the company's dedication to environmental responsibility.
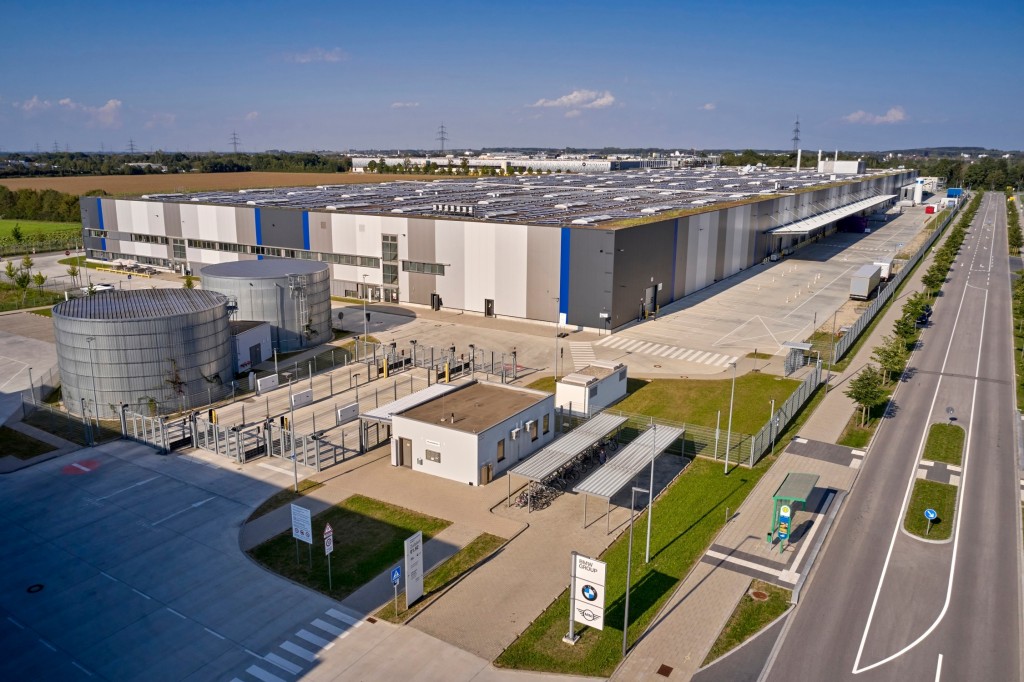
BMW's Parsdorf plant.